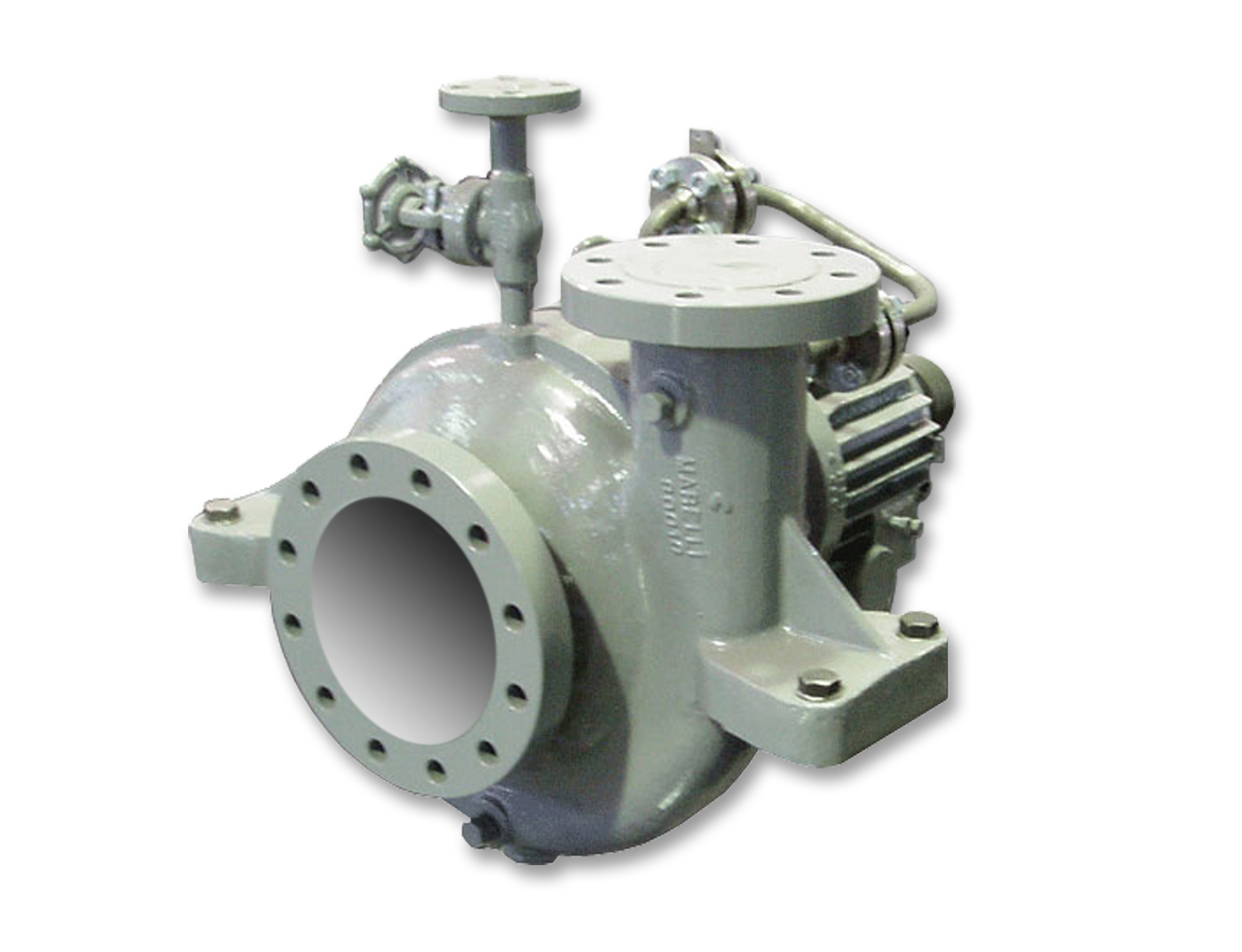
API-610 OH2 and ISO 13709 compliant for General Refinery Services centrifugal, single stage, full centerline mounted with high shaft rigidity for processes engineers requiring efficient high pressure and high temperature services
The Marelli SMK pump seres has a range of customized features to specific application requirements that process engineers require for upstream oil and gas, midstream, downstream refining, petrochemical and chemical processing.
- Flows to 7,000 gpm (1,600 m³/hr)
- Heads to 1,200 ft (256 m)
- Suction Pressure 551 psi (38 bar)
- Temperature Range -238 to 842°F (-150 to 450°C)
Precision engineered API/ISO 13709 process pumps meeting rigorous engineering requirements for heavy duty, high temperature applications while receding the total life cycle cost and improving mean time between repairs.
APPLICATIONS
Refineries
- Hydrocracking
- Topping
- Gas condensate
- HDS
- Merox LPG
- Amine
- Sour water
- Coking
- Platforming
Petrochemical
Crude oil and gas pipelines
Offshore and onshore oil and gas
Reverse osmosis
Synfuels
Proven to be reliable, efficient and long-lasting, Marelli OH2 pumps provide a number of operational benefits for process engineers and plant operators:
- API 610 11th Edition/ISO 13709 full compliance for reliability and accountability
- Suitable with 60 Hz and 50 kW motors
- Higher efficiencies due to a design with tangential discharge and a wide variety of hydraulics to match exact duty points
- Centerline mounted pump casing maintains alignment during operation and elevated temperatures
- Low suction specific speed and low NPSH characteristics with a wide choice of impellers for optimum efficiency over a large operating range
- Finned bearing housing to provide maximum heat dissipation under API 610 compliance
- Isolation chamber at bearing housing with a thermal barrier among mechanical seal chamber and bearing housing
- Deflection system with fins to improve cooling
- Labyrinth bearing seals to avoid external contamination and maximize seal and lubrication life
- Highly maintainable and replaceable wear rings to reduce overall life cycle costs
- Socket welded flanged drains and vents as standard (gussets and bracing also available)
- Choice of multiple impellers in each hydraulic pump casing for optimum efficiency over a wide operating range
- A variety of instrumentation options are available for monitoring all key operating perimeters (temperature, pressure, vibrations and more)
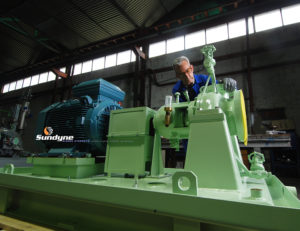
US 60 Hz
- Heads to 1,200 ft
- Flows to 7,000 gpm
- Standards API 610 OH2
- Maximum Motor Power 938 HP
- Temperature Range -238 to 842°F
- Maximum Case Working Pressure 725 psi
- Maximum Suction Pressure 551 psi
- Differential Head 1,200 ft
- Maximum Viscosity Consult Factory
- Mounting Configuration Horizontal-end top
- Seal Configurations API 682
- Available Flanges 300#, 600# ANSI FF/RF
- Suction and Discharge Sizes Up to 12″
- API Plans All API 682 Configurations
Metric 50 Hz
- Heads to 256 m
- Flows to 1,280 m3/hr
- Standards ISO 13709
- Maximum Motor Power 700 kW
- Temperature Range -150 to 450°C
- Maximum Case Working Pressure 50 bar
- Maximum Suction Pressure 38 bar
- Differential Head 360 m
- Maximum Viscosity Consult factory
- Mounting Configuration Horizontal-end top
- Seal Configurations API 682
- Available Flanges 300#, 600# ANSI FF/RF
- Suction and Discharge Sizes up to 30.48 cm
- API Plans All API 682 Configurations
Part | S1 | S5 | S6 | S8 | C6 | A8 | D1 |
Pressure Casing | Carbon Steel (A216 WCB) | 12% CHR | 316 AUS | Duplex | |||
Impeller | Cast Iron | Carbon Steel | 12% CHR | 316 AUS | 12% CHR | 316 AUS | Duplex |
Wear Rings | Cast Iron | 12% CHR Hardened | Hard-faced 316 AUS | 12% CHR Hardened | Hard-faced 316 AUS | Hard-faced Duplex | |
Shaft | Carbon Steel | AISI 4140 | 316 AUS | 12% CHR | 316 AUS | Duplex | |
Bearing Housing | Carbon Steel (A216 WCB) | ||||||
Base Gasket | AUS, Spiral Wound | 316 AUS Spiral Wound | AUS, Spiral Wound | 316 AUS, Spiral Wound | Duplex SS Spiral Wound |
Customized High Temperature Features
Cooled mechanical seal chamber
External cooling for bearing housing with finned heat exchanger fed with inert fluid and/or water
Convection venting for bearing housing with a low noise fan placed at the rear in the coupling side
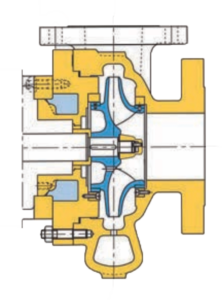
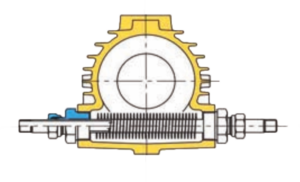
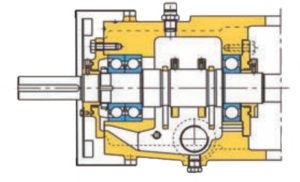
High Suction Pressure Options
Heavy duty bearing housings
Mechanical seals to meet safety and environmental requirements
Pump casing and seal chamber
Engineered bearings
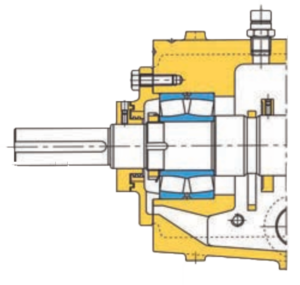
Lubrication System
- Purge ports with drain valve
- Test gauges for condition analysis
- Oil mist lubrication system with purge ports
- Outboard oil mist system for assuring flow through each bearing
For Coking Services
- Backwash system for wear rings and neck bushing
- Specific coke crusher available
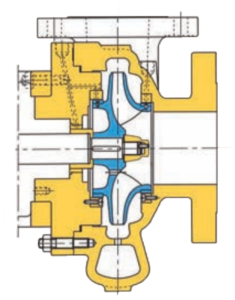
Baseplate Designs
- Pre-grouted and non-grouted for all driver types
- Special base designs to match oversize drivers, pump and turbines
- Tailor made baseplates available
- Skid mounting and oil field designs available